The Rise of Poland as a Manufacturing Center
It’s helpful to start with a little context.
Poland wasn’t always a popular country from which to source goods. In fact, in the 1990s and into the early 2000s, it was still seen by many as an Eastern Bloc country and risky to do business with. Not many steamship lines or importers wanted to go to Poland, thinking “If I send a container there, will I get it back?”
A poor road infrastructure made it even more difficult to move cargo out of Poland. Modern highways were few and far between, and trucks would regularly need to reroute to avoid low bridges.
That all began to change in 2004. Since then, the EU has poured billions of dollars into road and rail infrastructure improvements throughout the country. These days, it’s much easier to move cargo into and out of Poland. The following chart notes the top commodities exported from Poland to the US.
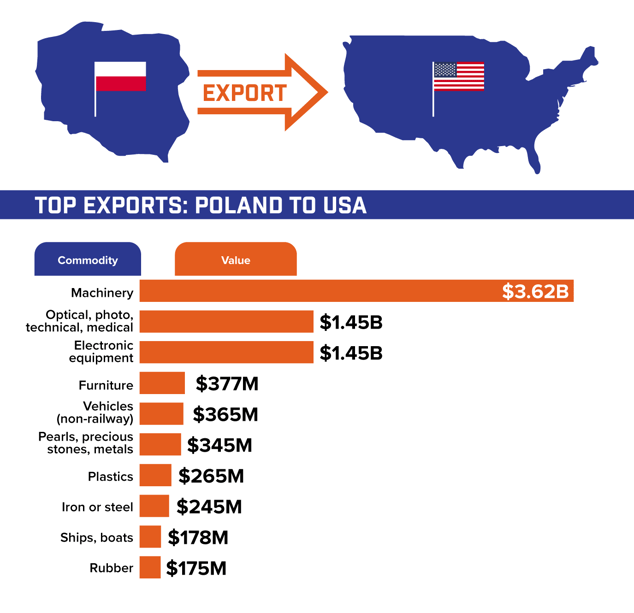
In addition to an improved infrastructure, several other benefits have fueled the rise of Polish manufacturing and the increased interest in Poland as a source of machinery, medical equipment, furniture, precious metals and other commodities (see chart):
- More reliable products. As a member of the EU, Poland accepted EU quality, technology and regulatory standards, which bolstered its reputation as a reliable manufacturing country. As a result, companies from around the world – including many American, German and UK manufacturers – have invested in new plants there, especially automotive and aerospace firms.
- Faster transit times. It takes about 20 days to ship containers from Poland to the US East Coast compared to a 30-day range for cargo originating in the Far East. That means less inventory and a faster cash cycle for companies that shift sourcing from the Far East to Poland – a huge supply chain advantage.
- Reduce sourcing costs. In addition to the cost advantages of getting high-quality products delivered faster, importers are also finding that Poland’s lower cost structure allows them to source goods for less than the cost of similar goods in Western Europe.
Since its entry into the EU, Poland has undoubtedly become a more powerful force on the world manufacturing scene.
The Impact of New Tariffs, And How to Mitigate Them
While Poland is not a major exporter of raw steel and aluminum, it does export many products that include those materials. Hundreds of such products are covered in Trump’s proclamation listing products now subject to 25% import duties.
Breaking out freight costs
One way to lessen the blow from the new tariffs for Polish exports to the US is to make sure to break out the cost of the ocean freight on the shipment’s commercial invoice. For example, if a product is valued at $25,000 and the cost of the ocean freight is $5,000, the total of $30,000 could be listed on the commercial invoice. If the freight is not broken out, the entire $30,000 could be subject to the 25% duty rate by customs, increasing your costs.
I.C.E. Transport also recommends packing as much product as possible into each container to reduce the number of containers you need to ship. By using this method, you could lower the number of containers by 20%, a considerable savings in freight costs. While this doesn’t address the tariff issue, it does help mitigate their impact.
I.C.E. president, Andrew Rozek, advises shippers to make sure the Harmonized System Code (HS code) on their products is correct. CBP inspectors are going to be extra diligent in scrutinizing shipments to check for violators under the new tariff schedule. By the same token, an incorrect HS code could also place a product on the 25% duty list that doesn’t belong there.
Getting a binding ruling on imported goods from CPB
You can have your customs broker apply to CPB on your behalf for a binding ruling. In effect, you’re petitioning the customs agency to classify, value, or apply duty rates to a product before it is imported. This ruling is legally binding for both CBP and the importer at all US ports of entry, ensuring consistency in customs treatment. In some cases, the ruling can result in a lower duty rate.
A binding ruling can cover:
- Tariff Classification: Determining the correct HS code and duty rate.
- Customs Valuation: Confirming the correct transaction value.
- Country of Origin: To determine if free trade agreements apply, or if the goods are subject to anti-dumping duties charged by CBP on goods it determines are sold at less than their US fair market value.
- Other Agreements and Regulations: Confirming whether a product qualifies for FTZ benefits, drawback, quotas, or special programs.
Rozek sounded a note of caution, however, on applying for a binding ruling. “It could go in your favor, or it could go against you,” he said. “You could win and come up with a lower duty or eliminate the tariff. But CPB could also issue a ruling that puts you in a different tariff category at a higher rate. Then it becomes a question of, do you want to challenge this further, or let it go? It's a double-edged sword.”
Identifying a Shipping Partner
Once you’ve decided to import from Poland, you’ll need to identify a shipping company. In our experience, about 70% of the time that decision is made in the US by the purchasing company, in accordance with Ex Works (EXW) Incoterms. Under EXW, the buyer is responsible for managing and paying for the transport of goods from the seller’s overseas factory.
If you ship via ocean container, the first thing you need to understand is that there is no direct ocean service from Poland to the US. You have two options:
- Load containers onto feeder vessels in the Polish port cities of Gdansk or Gdynia for shipping to a major Western European seaport, where goods are transloaded onto a container vessel bound for the US
- Truck containers directly to a major Western European seaport
The added level of complexity underscores the need for a reliable freight partner to ensure containers are not delayed as they move from port to port in different transport modes.
This is where the new ocean carrier alliances come into play. One result of the new alliance structure is that some carriers no longer have contracts with so-called “feeder vessel” lines that connect major and minor ports. The result is some disruption of service and delays between Poland and the US, at least temporarily.
Busy importers seeking a turnkey solution for international freight may be tempted to contract with a steamship line for door-to-door service. But that would be like booking your entire Hawaii vacation package – including hotel, local transportation and daily activities – with an airline. Steamship lines are not known for careful monitoring of door-to-door shipments, such as making sure a container does not sit for days at a transload point. For that, you need either a freight forwarder or an NVOCC that will monitor the entire move, from pick-up to final delivery.
NVOs offer more flexibility than forwarders for international moves. Unlike a freight forwarder, an NVO can issue its own bill of lading (BOL) for door-to-door service that is just as legal and recognized as the steamship line’s BOL.
While an NVO can rely on the line for port-to-port service, it can independently manage all other aspects of the shipment, including landside transport and customs clearance. The freight forwarder, on the other hand, can only book with steamship lines on a door-to-door basis and the cargo will travel on the line’s BOL. The forwarder can monitor the shipment, but it’s basically relying on the line to manage the entire move which, as we said, comes with service risks.
Bottom line: choosing an NVOC as your shipping partner will give you more flexibility to select the right solution for each aspect of the Poland-to-US shipment.
One other consideration is whether your US provider has an owned office vs. an agent in Poland. An agent may have 30 or 40 other customers vying for its attention on any given day and may be working with dozens of US forwarders to handle the transport and paperwork requirements at destination. By contrast, a logistics partner with owned offices in both the US and Poland, like I.C.E. Transport, will have a more integrated process and be far more focused on your freight and your total satisfaction.
Moving Freight from Factory to Port
When moving freight from a Polish factory to the origin port, you’ll need to decide whether the ocean shipment will originate in Poland (Gdansk or Gdynia) or from a major port in Germany (Hamburg, Bremerhaven), Belgium (Antwerp), or the Netherlands (Rotterdam). The decision will be driven by your preference for the lowest cost or the shortest transit time to the US from Poland.
You’ll save about a week to the Eastern US if you truck your goods directly to a Western Europe port. The closer your factory is to Poland’s western border with Germany, the cheaper it becomes. If you ship from Poland via a feeder vessel, it will take longer but you’ll save significantly compared to the direct truck to Germany. We find that most importers choose the lower-cost option, but there are times when speed trumps cost.
When moving freight to ports, you’ll have the choice of shipping via rail or truck. Like anywhere else in the world, rail will be cheaper in Poland, but also slower and less flexible. If your freight originates in Northern Poland nearer the ports, rail doesn’t make sense. But if freight originates in Southern Poland, home to most of the country’s manufacturing, rail is available directly to Gdynia or even German ports.
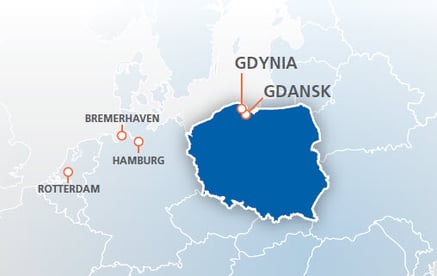
Trucking is often the better option to keep freight moving, particularly since a reduced rate is often available – provided you have a local logistics partner that can identify cost-saving freight opportunities. Because Poland is a smaller country, you often have truckers running southbound with a container from the port that needs to get back north. The large volume of one-way freight looking for backhauls keeps truck rates more economical.
Any shipment leaving Poland must go through export customs clearance. The rules for this are the same throughout the EU. The process is fully digitized and freight can be cleared anywhere, including inland customs offices, which are not used in the US. While such inland offices sound convenient, they can actually add time and distance to the journey when clearance can happen just as easily at the port.
How do ocean alliance changes affect shipping from Poland to the US?
Beginning in February 2025, there was a major realignment of ocean carrier alliances, precipitated by market dynamics and shifting business priorities. In the short term at least, it’s causing some disruption to sailings, including transit delays and shifts in port and terminal calls. Another new wrinkle: alliances are now more lenient in allowing members to partner with non-members, a factor that complicates scheduling and booking.
For shipments from Poland to the US, depending on vessel schedules, you could have a situation where a “feeder” vessel operator that used to ferry cargo from Gdansk or Gdynia to a major port such as Rotterdam or Hamburg no longer does so. At least for now, this could extend transit time by a few days or even a week, although new carrier/feeder partnerships will inevitably form to address these issues.
The good news is that an experienced NVOCC like I.C.E. Transport has strong relationships with both alliances and independent ocean lines. By working with them, shippers can make alternate bookings that reduce costly delays.
“If we see that there's a big connection gap with a certain alliance, we can shift to another carrier that matches up better and offers a shorter transit time,” Rozek said. “Or you could have ships calling on different terminals in the same port, adding to trucking costs. It’s that kind of knowledge that enables us to avoid those types of situations tied to a specific carrier or alliance.”
Managing US Customs and Paperwork
Nothing can derail an international freight shipment faster than mismanagement of US Customs and Border Protection (CBP)-related processes and paperwork.
It starts with submission of the Import Security Filing (ISF) by the customs broker on behalf of the importer of record. This is typically the US party responsible for filing the ISF and arranging customs clearance in the US, unless the purchase terms are Delivered Duty Paid (DDP). The ISF, also known as a 10 +2, contains important details on the shipment. CBP must receive the filing at least 24 hours before the container leaves the main shipping port bound for the US. Failure to file on time results in a $5,000 fine to the importer of record. A proactive shipping partner will monitor this closely and may even submit the data to the customs broker on your behalf.
When clearing Polish imports on the US side, you want a reliable customs broker that sees to all the details in a timely manner. Typically, the broker is only as good as the information it receives from the importer. Knowledgeable and proactive brokers can work with you to gather the necessary data.
Things get slightly more complicated if goods are purchased under DDP terms and the shipper is the importer of record. That leaves the Polish supplier with the uncomfortable task of finding a reliable customs broker in the US. In these situations – and even for all Poland-to-US freight – it can be easier to find an NVOCC that also offers customs brokerage services in both Poland and the US. Such logistics providers have influence on how customs clearances can be done on both sides and, as a result, can remove time and headaches from the import process.
The right customs broker can also help manage issues related to tariff schedules. The Harmonized Tariff Schedule (HTS), administered by the World Customs Organization in Brussels, is supposed to be universal, but that’s not always the case. When a number used in Poland does not have a corresponding US tariff number, it helps to have an experienced broker that will find a number that is not only accurate but could reduce duty charges.
Managing Landside Delivery
When it comes to landside delivery of Polish imports in the US, your choice of shipping partner will be very important. Unless you are a large-volume shipper, ocean carriers often do a poor job of managing the details associated with port pick-ups and final deliveries. Their strength is managing the ocean move.
A good example is heavyweight freight shipping. Ocean carriers regularly advise customers to limit container weights to 44,000 pounds, even though the legal limit is around 10,000 pounds above that. For shippers of dense freight (metal, beverages, knock-down furniture, etc), this means shipping up to 25% more containers than necessary – a six-figure hit to the profit line for many businesses.
Why do ocean carriers provide this advice?
Because heavy containers require specialized trucking partners for final port-to-consignee shipments – relationships that most ocean carriers lack. It’s simply more efficient for them when standard tractor-trailers can be used and no special arrangements are required. But those special arrangements can be the key to 5- and 6-figure savings, as this example shows.
Increased container weight the key ingredient for savings for importer of Polish flour
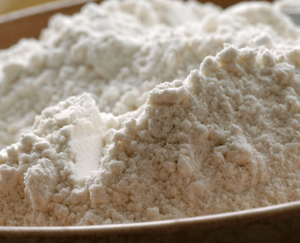
A small US importer of Polish flour was working directly with a steamship line to move about 24 containers a year – 509 bags per container – at a gross weight of 45,000 pounds per container. After consulting with the heavy freight shipping specialists at I.C.E. Transport, the company worked with its Polish supplier to reconfigure the bags and pallets to ship 940 bags in a single container weighing 53,400 pounds. By using I.C.E. to arrange door-to-door transport of these overweight containers, the importer began shipping the same volume of freight in four fewer containers per year, saving $13,600 – a nice profit increase for this small business.
5 Common Shipping Mistakes Made by Importers of Polish Goods
- Having Polish suppliers arrange transport. When suppliers control the freight, you are reliant on that company’s forwarder agreement. They make all decisions on transport type, speed and cost. What often happens is that, if you have questions or issues after the cargo sails, the shipper’s standard response is “call the steamship line.” In contrast, if you buy under Ex Works (EXW) purchase terms, you are always in control. Working with your freight forwarder, you decide how fast you ship, what you pay and what line to use. And you’re never in the dark about your shipment.
- Poor understanding of free time allowances. In recent years, we’ve seen steamship lines set free time terms different from those of the terminal receiving the container. For example, Maher Terminal at the Port of NY/NJ may allow containers to stay on port for 5 days, but under its contract with you the steamship line may charge a fee if you don’t pick up the container within 3 days. Meanwhile, the line’s agreement with the terminal is 5 days, so they pocket the payment difference. Make sure you work with a forwarder that stays on top of this issue, or your demurrage charges could skyrocket.
- Relying on the steamship line’s published transit times. These times are approximations only. Don’t make important sourcing decisions that rely on these published times. Many factors can contribute to delays, including a missed connection between the feeder vessel and the main trans-Atlantic sailing.
- Working with freight agents. If you are working with a US-based NVOCC that uses a freight agent in Poland, that agent is not going to care as much about your cargo as a company-owned office would. Typically, they book door-to-door moves with a steamship line and list the receiver in the US as the contact. Your customs broker is then stuck dealing with the lines, which traditionally offer poor customer service. If service is important to your freight operation, you are better off working with a forwarder that operates owned offices in both the US and Poland that will be accountable for all requirements and communications on both sides of the Atlantic.
- Not getting UL approval for electrical appliances. The importer, not the manufacturer, is responsible for ensuring that imported products comply with US standards for consumer safety. In Europe, the CE marking confirms that products meet the EU standard, but this is not recognized in the US. So, to avoid possible problems when entering the US, it’s best to get certified to the most common electrical standard from Underwriters Laboratories (UL).
Closing Thoughts: Speaking Straight from the Bridge
There are reasons why Poland is among the top 10 fastest-growing US trade partners. Among these:
- An excellent workforce that turns out high-quality products
- A lower cost structure that gives Polish manufacturers a price advantage over competitors in Western Europe
- Inbound transit times to the Eastern US that are at least 10 days faster than Asian imports
But to fully capitalize on these advantages, importers must have an effective and efficient inbound shipping solution – one that solves for transport and customs challenges commonly seen on Poland-to-US container freight. We hope this short guide helps you navigate some of these challenges.
We’ll end with some frank advice, with no sugar coating. Or, as they say in Poland, “mówić prosto z mostu” (speaking straight from the bridge). The answer for you could simply be a matter of finding a partner to do it for you – a logistics provider, like I.C.E. Transport, that manages a large volume of Poland-to-US freight and has seen and solved any of the Poland-related shipping challenges you are likely to face.
How many Poland shipping experts does it take to give you a competitive advantage?
Just one.